From the Drill Floor to the Derrick: Where Oil Rig Workers Face the Highest Risks
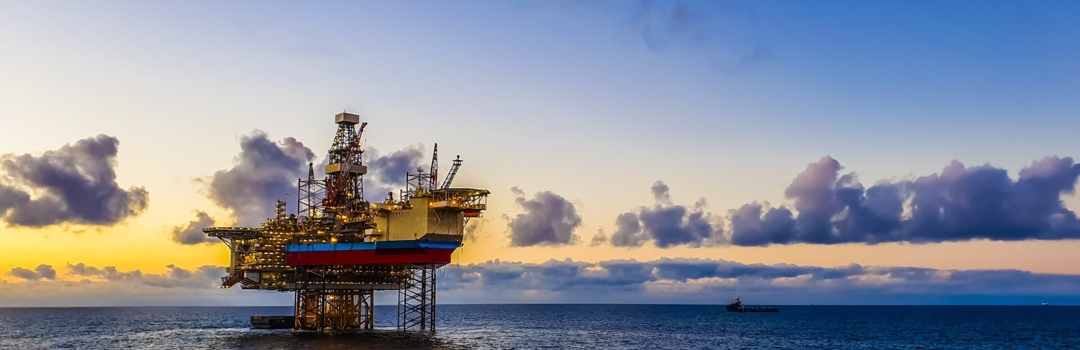
On April 20, 2010, the Deepwater Horizon offshore drilling rig exploded in the Gulf of Mexico, killing 11 workers and unleashing one of the worst environmental disasters in U.S. history. The blast was triggered by a failed blowout preventer, a last-resort safety device meant to seal the well in emergencies. Investigations later revealed a devastating pattern of cost-cutting, ignored safety warnings, and critical lapses in oversight. The equipment didn’t fail on its own. It failed because the companies responsible didn’t do enough to prevent it.
Offshore oil rigs are among the most dangerous workplaces in the world. Crews operate on remote, floating platforms where they contend with high-pressure systems, explosive gases, heavy machinery, extreme weather, and the ever-present danger of human error. Workers live and labor in tightly packed quarters. One mistake or one piece of neglected equipment can ignite a chain reaction with catastrophic consequences.
Danger in the Deep: What Makes Oil Rigs So Hazardous?
What makes oil rigs so treacherous isn’t just the nature of the work. It’s employers’ failure, time and time again, to take that danger seriously. There are far too many cases of rig workers, survivors, and grieving families who were told everything was safe—until it wasn’t. In many of these instances, the equipment itself was not to blame. The fault lay with employers who failed to properly maintain that equipment, skipped critical inspections, pressured crews to work faster, or ignored federal safety standards.
Sadly, when leadership prioritizes production over safety, workers pay the price.
Understanding which areas and pieces of equipment on oil rigs pose the highest risks is more than just a matter of awareness. It’s a matter of accountability. No matter their role, every oil rig crew member, from the drill floor to the derrick, faces unique hazards that require vigilance, training, and, above all, a company willing to invest in safety.
In this article, we examine where those dangers concentrate, from the towering derrick to the high-pressure pumps below deck. These aren’t just technical systems; they’re the very spots where workers’ lives hinge on split-second decisions and properly functioning machinery. When something goes wrong, the difference between survival and tragedy often comes down to whether the company chose to put people first.
The Drill Floor: Ground Zero for Serious Accidents
If there’s one place on an offshore rig where danger is constant, it’s the drill floor. This is the heart of the operation, the platform where drilling into the ocean floor actually happens. It’s also where the most serious injuries and fatalities often occur.
The drill floor is a tightly packed area filled with massive, fast-moving equipment. Pipes, cables, and heavy machinery are in constant motion, operated by roughnecks and floorhands who must remain alert, agile, and coordinated at all times. A single lapse, whether by man or machine, can result in life-changing injury or death.
Caught-In, Struck-By & Fall Hazards
Across the drill floor, workers face three main threats:
- Caught-in accidents from rotating or closing equipment
- Struck-by incidents involving swinging pipes, dropped tools, or moving parts
- Falls caused by slick surfaces, uneven footing, or sudden movement during operations
Often referred to as “the big three,” these risks don’t come from faulty machinery alone. In many cases, injuries occur when employers fail to train workers on how to safely interact with automated equipment, enforce lockout/tagout procedures during maintenance, provide adequate protective gear, or maintain grip surfaces and fall protection systems.
Rotary Tables & Drill Strings
At the center of the drill floor is the rotary table, which turns the drill string, a connected series of pipes that extend down into the well. This equipment operates at extremely high torque and speed. If a worker gets caught in the rotating mechanism, the result can be catastrophic.
Even seasoned workers have suffered entanglement injuries, including crushed limbs and amputations, after coming into contact with the spinning drill string. These injuries often occur during maintenance or pipe handling when protective guards are removed or when crews are under pressure to keep drilling operations moving.
Top Drive Systems
Mounted above the rotary table is the top drive, a powerful piece of machinery that moves the drill pipe up and down. While it allows for faster, more precise drilling, the top drive also introduces vertical motion that can become deadly if a failure occurs or someone is standing in the wrong place at the wrong time.
A top drive malfunction or miscommunication during pipe handling can result in falling pipes, struck-by incidents, or crush injuries. The sheer weight of the equipment—often thousands of pounds—means that accidents are rarely minor.
Drawworks & High-Tension Cables
To raise and lower heavy drill pipe, the rig relies on drawworks, a system of winches and motors that operate steel cables under extreme tension. These cables, often stretching from the floor to the top of the derrick, carry immense loads.
When a cable snaps or a brake fails, it unleashes violent, whipping force. Workers have been struck, crushed, or decapitated by recoiling lines. The risk is especially high when workers stand too close during tripping operations, which is the process of pulling pipe out of the well.
These incidents are preventable. Routine inspections, proper tensioning, and adequate communication protocols must be in place to reduce the risk to workers. Yet some employers neglect regular maintenance, leaving aging cables in use well past their safe lifespan. Unfortunately, it’s workers who suffer the consequences of this negligence.
Catwalks & Pipe Racks
Just off the drill floor are catwalks and pipe racks, where crews store and maneuver the massive steel pipes used in drilling. Using automated or manual pipe-handling systems, workers position these 30- to 40-foot-long pipes for connection to the drill string.
Despite automation, pipe handling remains one of the most dangerous parts of offshore work. A single miscalculation can send pipes sliding, falling, or swinging unexpectedly, leading to crushing injuries, fractured skulls, and fatalities.
What’s more, the design of some catwalks forces workers into awkward positions, standing on slick steel, sometimes with poor visibility and limited escape routes. When these factors are combined with other risk factors, like fatigue or rushing, hazards are amplified.
Above the Floor: The Derrick, Crown Block & the Risk of Falling Loads
While the drill floor is dangerous at eye level, the threats above it are just as deadly—and often even less forgiving. Towering above the rig is the derrick, a massive steel structure that supports the heavy lifting equipment needed to move drill pipe in and out of the well. This vertical system includes the crown block, traveling block, and hoisting cables. Each one of these is critical to the rig’s function, and each is capable of causing fatal accidents if safety protocols are ignored.
High Stakes at High Altitudes
The derrick is more than just a steel tower; it’s a workplace. Derrickmen are some of the most skilled and vulnerable workers on the rig. They climb to platforms hundreds of feet in the air to guide pipe into place and monitor drilling fluid returns. Working at these heights means that even minor errors can result in catastrophic falls.
Fall protection systems are not optional—they are essential lifesavers. But to be effective, these systems must be:
- Properly anchored and regularly inspected
- Paired with rigorous training on fall-arrest procedures
- Used with reliable rescue plans in place for emergencies
When any of those elements are missing, or when workers are rushed or fatigued, falls can happen. And on an offshore rig, there’s often no second chance.
Crown Blocks & Traveling Blocks
The crown block sits at the very top of the derrick, supporting pulleys that guide steel cables across the structure. The traveling block moves vertically, lifting and lowering drill pipe, sometimes hundreds of tons at once.
If the hoisting system fails, whether due to overloading, brake malfunction, or frayed cables, massive blocks of steel or pipe can plummet without warning. Workers below may have no time to react. This danger is not hypothetical. In multiple fatal offshore incidents, dropped blocks have crushed workers, destroyed equipment, or damaged structural components, sometimes triggering chain-reaction failures throughout the rig.
The Derrickman’s Platform
Perched near the top of the derrick, the derrickman’s platform is where pipes are guided into place and mud levels are monitored. It’s a job that requires strength, precision, and incredible balance, especially during bad weather.
The platform is often narrow, with minimal space to move. A sudden gust of wind, a misstep, or a mechanical jolt can be fatal.
To safeguard workers, employers must ensure that:
- Guardrails, harness systems, and secure platforms are maintained
- Derrickmen are well-rested and not pushed beyond safe working hours
- Operations pause during severe weather or mechanical uncertainty
Unfortunately, some companies push ahead even when conditions are clearly unsafe, risking lives in the name of production quotas.
Struck-By & Crushing Hazards from Above
One of the most alarming realities of derrick work is that a worker can do everything right—follow every procedure, wear every piece of protective gear—and still be killed by equipment falling from above.
These are not rare occurrences. From January 2015 to July 2022, the oil and gas extraction industry reported 2,101 severe work-related injuries to the Occupational Safety and Health Administration (OSHA). And, according to the Dropped Objects Register of Incidents Statistics (DORIS), falling or dropped objects remain among the top three most common causes of serious injuries or fatalities.
The towering structures above the drill floor may seem stable, but they demand constant vigilance. When companies neglect inspections, skip maintenance, or push workers to take risks, the consequences are rarely minor.
Pressure Below: The Blowout Preventer, Mud Pumps & the Hidden Forces Underground
Working on an offshore rig means facing various dangers not just above deck but also deep beneath the seafloor. Hidden underground forces, like high-pressure gas, volatile fluids, and unstable geologic formations, can create a minefield of hazards. The equipment designed to manage these forces is absolutely critical to keeping rig crews safe. When it fails, the consequences are often catastrophic.
Blowout Preventers (BOPs)
The blowout preventer, or BOP, is one of the most vital pieces of safety equipment on an oil rig. It’s designed to seal off the wellbore in the event of an uncontrolled surge of oil, gas, or other fluids, commonly referred to as a blowout. The BOP can weigh up to 400 tons and sits atop the wellhead, ready to shut in the well during a crisis. When it works, the BOP prevents deadly pressure surges from reaching the rig floor. When it doesn’t, the results can be devastating.
One of the most notorious failures in BOP history occurred during the Deepwater Horizon disaster in 2010. The rig’s blowout preventer failed to activate, allowing a blowout to ignite a massive explosion that killed 11 workers and released nearly 5 million barrels of oil (134 million gallons) into the Gulf of Mexico. Investigations later revealed serious flaws in the BOP’s design and maintenance—failures that might have been caught with proper inspection and oversight.
The Deepwater Horizon is an extreme example, but it’s far from isolated. Blowouts, even on a smaller scale, can cause fatal burns, gas inhalation, or drownings if the rig floods.
High-Pressure Mud Pumps
Drilling fluid—commonly called “mud”—is continuously pumped down the drill string to cool the bit, maintain pressure, and bring cuttings back up to the surface. This process is powered by mud pumps, which operate at thousands of pounds per square inch (PSI). These are powerful, high-volume machines, often capable of moving hundreds of gallons of fluid per minute.
If a hose bursts or a valve fails under pressure, mud can be ejected with tremendous force. Workers have suffered blunt-force trauma, chemical burns, and inhalation injuries from sudden releases. In some tragic cases, workers have been struck in the head or chest by metal debris or high-pressure fluid when a component failed unexpectedly.
Shale Shakers
After mud returns to the surface, it passes through shale shakers, vibrating screens that filter out rock cuttings and debris. Though somewhat less dangerous than a BOP or mud pump, shale shakers are one of the most overlooked hazards on the rig.
The constant movement of the screens and high-speed vibrations create significant entanglement risks. Workers inspecting or cleaning the equipment can be pulled into moving parts if proper lockout/tagout procedures aren’t followed. Hands, clothing, and even entire limbs have been caught in shaker components.
These machines also produce fine particles and vapors from the mud, which can lead to chemical exposure over time if respiratory protection isn’t used properly.
Heavy Lifting: Cranes, Hoists & the Danger Overhead
On an offshore oil rig, the airspace above isn’t just open sky; it’s a high-risk zone filled with heavy swinging loads, steel cables under tension, and massive pieces of equipment being lifted and positioned. The potential for disaster increases with every ton of gear that moves overhead.
Cranes & Winches
Deck cranes are used daily to load and unload supplies, move pipes, and assist in drilling operations. These machines lift thousands of pounds at a time—often with workers standing just feet away. A mechanical failure, miscommunication, or an improperly secured load can become fatal in an instant.
Winches and wire ropes are also vital to oil rig operations. They are used to pull and position materials across the deck, but these cables are often under extreme tension. When one snaps, it can recoil like a whip, striking anyone in its path with deadly force.
These accidents are avoidable with proper maintenance, inspections, and adherence to safety protocols. When companies rush operations or skip steps to save time, even minor oversights can become lethal.
Falling Loads, Crushing Hazards & Visibility Issues
Crane operations often occur in areas with limited visibility due to fog, rain, and sea spray, all of which can be worsened when work is carried out at night. Without clear communication between crane operators and deckhands, or without effective signaling protocols in place, workers can easily find themselves under a suspended load or in a crush zone.
Tragically, workers can be struck by swinging equipment or pinned between pipes when employers or supervisors fail to enforce basic safety practices, like using spotters or keeping personnel clear of lift zones. As a result, they may suffer catastrophic or even fatal injuries.
Emergency Equipment, Transportation & Safety Systems Must Work
Unlike land-based worksites, offshore rigs operate miles from shore, with no easy access to hospitals, fire departments, or emergency services. The isolated nature of these jobsites makes preparedness and redundancy absolutely critical. When companies fail to invest in reliable safety systems, workers can find themselves stranded and facing injury or death without any way to escape.
When Life-Saving Equipment Fails
Lifeboats, escape pods, fire suppression systems, and emergency breathing gear are all designed to protect workers when the worst happens. But when this equipment is poorly maintained or outdated, it can actually worsen the danger.
In some cases, workers have been unable to launch lifeboats during a fire or explosion because mechanisms were corroded or non-functional. In other instances, faulty fire suppression systems have allowed fires to rage uncontrollably, endangering the entire crew.
Companies often argue that “the equipment failed,” but the truth usually goes deeper. All too often, these entities fail to test, inspect, or update equipment properly, sometimes for years. When an emergency strikes, poorly maintained life-saving equipment can become useless, leaving workers without any options.
The World’s Most Dangerous Commute
Offshore oil rigs are among the most remote jobsites, and getting to work typically involves a dangerous commute. Many employees are brought to oil rigs by helicopter or crew boat. These modes of transportation carry their own set of serious risks.
Offshore workers can be severely injured or killed during these trips, particularly when operators are unqualified or equipment is not properly maintained. And these incidents are not as uncommon as many people believe.
On April 1, 2009, Bond Offshore Helicopters Flight 85N plunged into the North Sea, killing all 16 people aboard. The aircraft had been transporting KCA Deutag Drilling employees from the BP oil platform in the Miller oilfield when it went down as a result of a “catastrophic failure of the main rotor gearbox,” according to an investigation by the Air Accidents Investigation Branch (AAIB). This was the second Bond Offshore Helicopters crash in less than two months, with another flight ditching in the North Sea on February 18. In that case, all 18 passengers and crew were rescued.
In perhaps one of the most tragic of these incidents in recent years, the Seacor Power, a lift boat tasked with bringing crewman and cargo to an oil rig in the Gulf of Mexico, capsized due to severe weather. Only six of the vessel’s 19 crewman survived, and seven of the 13 victims were never recovered.
These are just a few examples of the countless instances in which oil rig workers’ lives were at risk just getting to the jobsite. Though the commute is inherently dangerous, no job is worth a life. When transportation companies cut corners, ignore safety standards, and skip critical maintenance, they must be held accountable.
Offshore Dangers Demand Onshore Accountability
The dangers of offshore oil work aren’t simply “part of the job.” They are the direct result of negligent choices made by employers, contractors, and equipment manufacturers—choices to cut corners on inspections, to delay safety upgrades, to silence workers who raise concerns, and to prioritize production over protection.
Every time a blowout preventer fails, every time a crane drops a load, every time a lifeboat won’t launch, there is a chain of decisions that led to that failure. At Arnold & Itkin, we’ve helped hundreds of offshore workers and their families uncover the truth behind these incidents. We’ve seen firsthand how preventable these tragedies truly are when employers take their responsibilities seriously.
The equipment on an oil rig may be complex, but the duty of care is simple: Companies must take absolutely every reasonable precaution to protect the lives of those they send offshore. Anything less is unacceptable.
- Categories