Most Common OSHA Violations
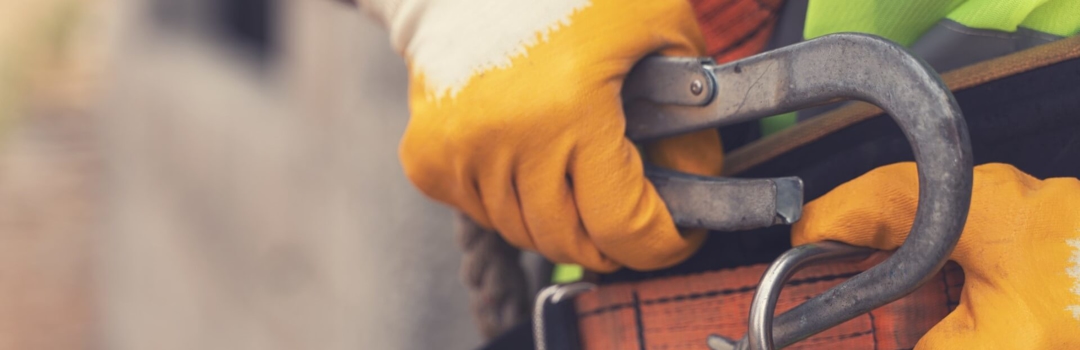
While any worker in any field could be injured on the job, there are some industries and occupations that are more dangerous than others. The Occupational Safety and Health Administration (OSHA), the government agency responsible for creating and enforcing safety standards to protect workers from occupational injuries, tracks the number of citations it issues for various violations. Reviewing the most common OSHA violations gives one a clear picture of which workers are at risk and why.
Each year, OSHA releases a list of the 10 most common citations given by its inspectors for workplace safety code violations. OSHA releases this list of citations because the administration hopes that employers make changes in the workplace to protect their employees from serious injuries and death.
The most recent list of top OSHA violations applies to the fiscal year 2024, from October 1, 2023, to September 30, 2024.
The top 10 OSHA citations in 2024 were:
- Insufficient fall protection (general requirement violations)
- Improper hazard communication (general industry)
- Lack of proper hazardous energy control (lockout/tagout procedures)
- Ladder safety violations (construction)
- Insufficient respiratory protection (general industry)
- Powered industrial truck violations (general industry)
- Lack of adequate fall protection training (construction)
- Scaffolding violations (construction)
- Improper eye and face protection (construction)
- Insufficient machine guarding (general industry)
Year to year, the top workplace safety violations reported by OSHA are generally quite similar. Some will move higher on the list than others from one year to the next, but the top 10 usually remain somewhat the same.
The Top Five OSHA Violations: Taking a Closer Look
Inadequate fall protection, poor hazard communication, improper lockout/tagout procedures, unsafe ladders, and lack of respiratory protection are consistently among the most frequently cited OSHA violations. Here, we take a closer look at these safety standards and how violations put workers at risk.
Fall Protection
OSHA’s “duty to have fall protection” (Standard 1926.501) rule requires employers in construction and other industries to protect workers from falls when they are working six feet or more above a lower level. Employers must ensure that the surfaces workers walk or work on are strong enough to hold them safely.
Depending on the situation, protection can include:
- Guardrails
- Safety nets
- Personal fall arrest systems
- Covers over holes
If using standard fall protection isn’t possible or creates more danger, employers must create a detailed safety plan that follows specific OSHA rules. The goal is always to prevent falls and falling object hazards before they cause injury or death.
Despite these strict regulations, fall protection violations consistently remain one of the most common types of OSHA violations reported each year. This often equates to employers failing to provide or maintain adequate fall protection gear, such as railings and fall arrest systems for employees working at heights.
Sadly, this lack of adequate fall protection often leads to catastrophic injuries and workplace fatalities. Falls, especially falls from significant heights, is one of the leading causes of death among U.S. workers.
Hazard Communication
OSHA’s “hazard communication standard” (Standard 1910.1200) ensures that workers know about the chemicals they may be exposed to on the job and how to stay safe. It requires chemical manufacturers and importers to classify hazards and share that information through labels, safety data sheets, and training. Employers must maintain a written hazard communication program and make sure workers understand the risks and how to protect themselves. This standard follows global guidelines for consistency and safety.
Chemical safety in the workplace is crucial for the well-being of every person at the site. To remain in compliance, OSHA requires employers to label chemicals (including mixtures) and to train workers on how to properly handle chemicals.
Some examples of common hazard communication violations include instances in which employers:
- Fail to label hazardous chemicals
- Label chemicals improperly
- Fail to use or update safety data sheets
- Classify chemicals improperly
- Fail to provide adequate employee training
The consequences of these violations can be severe, often leading to serious workplace accidents, injuries, and even fatalities. Sadly, this remains one of the most common types of OSHA violations year after year.
Hazardous Energy Control (Lockout/Tagout)
OSHA’s hazardous energy control, or lockout/tagout, standard (1910.147) protects workers by requiring employers to prevent machines and equipment from starting up unexpectedly during maintenance or servicing. The rule mandates that hazardous energy sources (like electrical, mechanical, hydraulic, or pneumatic) be isolated and locked or tagged out before work begins.
Employers must create detailed procedures, provide training, and ensure only authorized employees can apply or remove these safety devices. Lockout (using physical locks) is preferred, but tagout (using warning tags) may be used if it offers equivalent protection. The goal is simple: stop machines from turning on when someone could get hurt.
Unfortunately, improper lockout/tagout procedures are common in workplaces across the U.S. This frequently leads to catastrophic injuries, such as amputations or crush injuries, machine entanglement, and death.
Ladders
While they are valuable pieces of equipment in many industries, ladders can cause serious injuries or even death if they are used improperly. Employers have an obligation to properly train employees in ladder safety and to ensure ladders are in proper working order.
Under OSHA Standard 1926.1053 (ladders), all ladders, including job-made ladders, must meet certain design specifications and be able to withstand specific loads without failing. For example, typical self-supporting portable ladders must be able to support at least four times the maximum intended load and fixed ladders must be able to support at least two loads weighing 250 pounds each. Further specifications regulate various aspects of ladder rungs, steps, and cleats, including the position and spacing of these elements.
When ladders fail to meet OSHA standards, workers are at risk of serious falls and other accidents. This can—and often does—have devastating consequences. According to the Centers for Disease Control and Prevention (CDC), more than half a million (500,000) people in the U.S. are treated for ladder-related injuries each year, and approximately 300 people die due to falls from ladders and other related incidents.
Respiratory Protection
Millions of American workers wear respirators on the job. They are meant to provide protection from harmful substances and environments where workers would not get enough oxygen without them.
Because properly functioning respirators are so important, OSHA has set standards to regulate their use. Under Standard 1910.134 (Respiratory Protection), employers must provide appropriate respirators to employees when the use of this equipment is necessary to protect employee health and safety. Additionally, employers must establish and maintain a respiratory protection program that outlines specific worksite procedures and elements for respirator use. The program must be provided in writing and continuously updated as necessary to reflect any changes in the workplace that affect required respirator use.
Respiratory protection violations are among the most common OSHA violations in the U.S. each year.
These violations occur when employers:
- Fail to provide employees with respirators
- Do not provide the right type of respirators for employees
- Use or provide defective respirators
- Do not properly train employees on respirator use
Such violations can have both short- and long-term consequences for workers, including a wide variety of adverse health effects. In some cases, occupational respiratory disease may not become apparent for years, making it even harder for workers to prove the connection between their work and their illness.
OSHA’s Role in Reducing Workplace Fatalities
While some employers may view OSHA requirements as tedious and expensive, they exist for valid reasons. Before the government created OSHA in 1970, the American workplace was facing a health crisis. After nearly 100 years of industrial growth, government leaders realized that the integrity of the massive United States economy depends on the well-being of the workers who made it so successful.
While worker fatalities have improved since the earliest days of the 19th century’s Industrial Revolution, serious injuries and fatalities are still occurring at an alarming rate. In 1970, about 38 workers died each day in the United States. As of the most recent statistics, OSHA estimates that its regulations have helped lower the U.S. occupational fatality rate to about 15 each day. The organization also advertises that it has lowered the injury and illness rate of United States workers from 10.9 per 100 to 2.8 per 100 over the last four decades of its existence.
Safety standards and regulations are a big part of this. Without them, workers face significant risks to their health, safety, and lives. This is why it is so important that employers follow OSHA standards and that violations are not tolerated.
If your employer failed to provide a safe work environment, call our work injury attorneys today at (888) 493-1629. We've won billions for clients and only collect fees if we win results!