When Dust Turns Deadly: A Comprehensive Guide to Workplace Dust Explosions
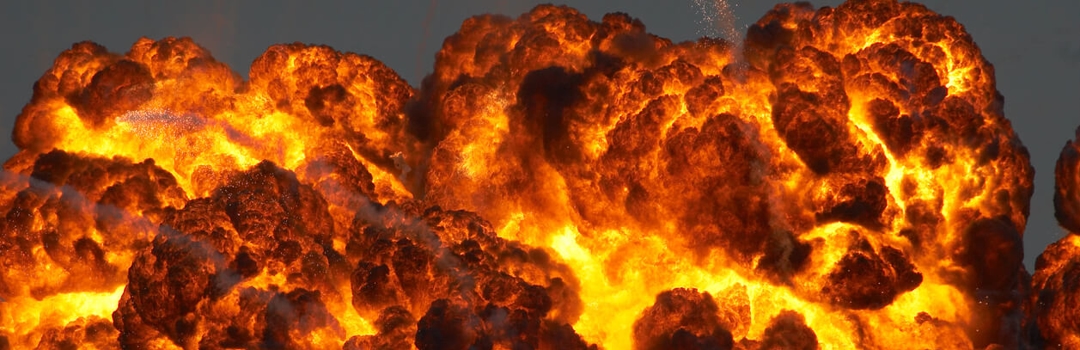
Dust might seem harmless, nothing more than an inevitable byproduct of industrial work or agricultural processing. But under the right conditions, this ordinary material can become a lethal threat. Dust explosions are sudden, violent, and devastating events that often occur without warning—and they are not rare. Every year, workplace dust explosions cause catastrophic injuries, fatalities, and millions of dollars in damage.
While grain dust explosions may be the most well-known type of these disasters, the truth is that combustible dust exists in a wide range of industries, from food processing and woodworking to pharmaceuticals and metal fabrication. Wherever fine particles are suspended in the air and an ignition source is present, the risk of an explosion becomes very real.
These incidents are rarely “accidents” in the true sense of the word. Dust explosions are preventable and are often the result of overlooked safety standards, inadequate maintenance, or systemic negligence. When employers, manufacturers, or third-party contractors fail to recognize and mitigate these hazards, the consequences can be catastrophic—and those responsible must be held responsible. No matter what.
What Is a Dust Explosion?
A dust explosion is a rapid combustion event that occurs when fine, combustible particles are suspended in the air in a confined space and exposed to an ignition source. Unlike an open fire or a flash fire, a dust explosion generates an extremely high-pressure shockwave, often strong enough to destroy industrial facilities and seriously injure or kill those nearby.
One of the things that makes dust explosions particularly dangerous is that the material involved doesn’t appear hazardous on its own. Ordinary substances—like grain, flour, sugar, wood dust, metal shavings, or powdered plastics—can become explosive when ground into fine particles and dispersed into the air.
Some common materials that can cause dust explosions include:
- Aluminum
- Coal
- Grain
- Fine powders
- Magnesium
- Metals
- Pharmaceuticals
- Plastic
- Rubber
- Sugar
- Textile fibers
- Wood
The Dust Explosion Pentagon
At the heart of every dust explosion is a specific combination of factors known as the “dust explosion pentagon.” This refers to the five key elements that must be present for a dust explosion to occur.
The five elements of the dust explosion pentagon are:
- Combustible Dust – A fuel source, such as organic or metallic dust, that can ignite
- Oxygen – Present in the air and essential for the combustion process
- Dispersion – Particles must be suspended in the air at the right concentration
- Confinement – An enclosed or semi-enclosed space that allows pressure to build
- Ignition Source – Heat, flame, static electricity, friction, or even a hot surface
When these elements combine, the result can be a primary explosion, or a sudden ignition of airborne dust in a localized area. But often, the primary explosion is just the beginning.
As the blast stirs up settled dust throughout the space or wider facility, it creates a much larger cloud of combustible material. If this cloud ignites—which often happens just seconds after the initial blast—it can trigger a secondary explosion. Secondary explosions are usually far more destructive than the primary blast, ripping through entire buildings and causing the majority of injuries, fatalities, and structural damage.
Secondary explosions are also entirely preventable. Proper housekeeping, dust control systems, and safety protocols can eliminate the buildup of settled dust that fuels these larger-scale events. Unfortunately, when employers cut corners or ignore safety standards, the consequences can escalate quickly.
If Dust Explosions Are Preventable, Why Do They Happen?
Dust explosions remain a significant concern in agricultural and industrial industries. According to the U.S. Chemical Safety Board, between 1980 and 2005, there were 281 combustible dust incidents in the United States, resulting in 119 fatalities and 718 injuries. And a report by Purdue University found that, on average, there were about 8.4 dust explosions per year nationwide from 2013 to 2023.
Dust explosions are not random accidents; they are usually the result of identifiable and preventable factors. Despite established safety protocols and regulatory guidelines, dust explosions continue to happen, particularly in certain industrial settings.
Several industries are particularly susceptible to dust explosions simply due to the nature of their operations. These industries include:
- Agriculture: Grain elevators, storage silos, and feed mills can accumulate dust from crops. These areas are also inherently enclosed or semi-enclosed, making the risk of an explosion even higher.
- Food Processing: Facilities handling sugar, flour, and spices often have dust and other fine particulate matter in the air. This heightens the risk of explosions, especially when dust is present in enclosed spaces.
- Woodworking: Sawmills, furniture manufacturing facilities, and other woodworking environments generate substantial amounts of wood dust, a known hazard. Heat or sparks from woodworking equipment can lead to explosions.
- Metalworking: Operations involving aluminum, magnesium, or titanium can produce explosive metal dust. These incidents tend to be especially catastrophic due to the dispersion of burning metal or molten particles.
- Chemical Manufacturing: Processes like powder handling and transfer can increase the risk of dust explosions in chemical manufacturing settings, often leading to catastrophic injuries and loss of life.
Within these industries, there are many risk factors that increase the likelihood of dust explosions.
Some of these risk factors include:
- Poor Housekeeping: Insufficient cleaning or facility upkeep can lead to dust accumulation. This dust can become airborne and ignite.
- Inadequate Ventilation: Without proper airflow, airborne dust concentrations can reach explosive levels.
- Lack of Maintenance: Without regular inspections and maintenance, industrial equipment can malfunction. This may provide ignition sources.
- Insufficient Training: When employees are unaware of dust hazards, they may inadvertently create dangerous conditions.
Notable Case Studies
Every year, workers are injured and killed by dust explosions. Throughout history, the U.S. has been home to some of the worst dust explosion disasters.
The Imperial Sugar Refinery Explosion (2008)
On February 7, 2008, an explosion occurred at an Imperial Sugar refinery in Port Wentworth, Georgia, killing 14 workers and injuring 36 more. A report by the U.S. Chemical Safety Board (CSB) determined that the incident was “entirely preventable.”
According to investigations by CSB and the Occupational Safety and Health Administration (OSHA), several factors contributed to the deadly explosion, including poor housekeeping that led to large accumulations of sugar dust. After the initial blast, this dust became airborne and led to numerous secondary explosions, which spread rapidly throughout the facility.
The factory’s outdated construction was also believed to have led to the severity of the explosion and resulting fire. Not only did the building have a wooden ceiling, but it also contained a type of creosote commonly referred to as “fat lighter” due to its known fire risk. This creosote was widespread throughout the facility and likely contributed to the severity and rapid spread of the fire.
The West Pharmaceutical Services Explosion (2003)
On January 29, 2003, a catastrophic explosion ripped apart a West Pharmaceutical plant in Kinston, North Carolina. The blast, which was the result of excess dust accumulation in the ceiling, killed 6 people and injured 36 more, including two firefighters.
An investigation by the Chemical Safety and Hazard Investigation Board found that the facility’s ventilation system pulled dust up into the ceiling where it had accumulated at a thickness of about 0.25 to 0.5 inches. This dust was disturbed, became airborne, and ignited, leading to the massive explosion that destroyed the building and sent debris flying up to two miles away.
The ignition source for the blast was never officially discovered, but it was likely one of five possible things: a rubber coating machine that had operated around the clock nearly every day of the week for the past 16 years and which had had numerous internal fires, an overheated batch of rubber that ignited, a light fixture or electrical ballast that ignited, an electrical fault, or an air cooling duct that fed an electric motor. Workers at the plant had also noted accumulated dust prior to the incident but were unaware of how dangerous it was.
AL Solutions Plant Explosion (2010)
On December 9, 2010, three workers lost their lives and one other was injured when an explosion occurred at an AL Solutions metal recycling plant in New Cumberland, West Virginia. The secondary blast was powerful enough to blow off part of the roof and could be heard a quarter of a mile away.
A report by the U.S. Chemical Safety Board found that dust produced from the milling and processing of titanium and zirconium ignited when a poorly maintained metal blender became hot and/or produced sparks as a result of metal-on-metal contact. Although the metal blender had a cover that was meant to stop fine particles from dispersing, it was discovered that this cover was often left open while the metal blender was in use.
Further investigation found that, although most of the plant employees were aware of the combustible nature of dust, they did not receive adequate safety hazard training and, as a result, did not fully understand the dangers present. Furthermore, the plant operators did not enforce compliance with safe handling standards for metals like titanium and zirconium. This led to many safety protocols—such as closing the cover of the metal blender—being ignored.
Regulatory Oversight & Compliance Challenges
While agencies like the Occupational Safety and Health Administration (OSHA) and the National Fire Protection Association (NFPA) provide guidelines for managing combustible dust, enforcement can be inconsistent. OSHA's Combustible Dust National Emphasis Program aims to identify and mitigate dust hazards, but without a specific federal standard, compliance with this program varies. Meanwhile, the NFPA's standards, such as NFPA 654, offer comprehensive safety measures, but they are not legally binding unless adopted by local jurisdictions.
The lack of widespread mandatory regulations and the reliance on voluntary compliance with dust hazard safety guidelines contribute to ongoing vulnerabilities in agricultural and industrial settings. In many cases, employers fail to implement or enforce proper safety standards, ignore regulatory guidelines, or neglect to provide employees with adequate training. Tragically, the consequences are often devastating.
Preventing Dust Explosions: Employer Responsibilities & Worker Rights
Employers play a critical role in preventing dust explosions. Because these incidents are largely avoidable, regulatory agencies and safety organizations place a high burden of responsibility on facility owners, operators, and managers to recognize risks and implement control measures. Failing to do so not only endangers lives but can also result in significant legal and financial consequences.
To protect workers and reduce the risk of catastrophic explosions, employers must take a comprehensive, proactive approach that includes hazard assessments, engineering solutions, operational practices, and employee education.
1. Hazard Assessments & Dust Hazard Analysis (DHA)
Identifying and evaluating potential hazards is a foundational step in any dust explosion prevention plan.
This includes conducting:
- Dust hazard analyses (DHAs), as outlined in NFPA 652, which requires facilities to systematically identify and assess combustible dust risks.
- Testing the combustibility of various materials to determine if they pose an ignition or explosion hazard.
- Regular risk assessments to review work processes, housekeeping practices, and any changes in materials or equipment.
These procedures are not a one-time requirement; dust hazard analyses and risk assessments must be updated when significant changes occur in the facility or operational processes. Combustibility testing should be done regularly, particularly when new materials or processes are introduced.
2. Engineering Controls
Engineering controls are physical systems and design features that reduce the likelihood of dust ignition and explosion.
Examples of engineering controls include:
- Dust Collection Systems: Properly designed and maintained dust collection systems help remove airborne dust before it can accumulate at hazardous levels.
- Local Exhaust Ventilation (LEV): These systems capture dust at the source, minimizing dispersion into the broader workspace.
- Isolation Barriers: Physical separation between dust-generating processes and ignition sources can prevent chain reactions.
Engineering controls are among the most effective lines of defense, but they must be properly installed, maintained, and monitored.
3. Housekeeping & Maintenance
Even the best-engineered systems can fail if facilities are not kept clean and equipment is not regularly serviced.
To combat this, employers must implement:
- Routine Cleaning Protocols: Employers should implement and enforce daily and weekly housekeeping plans to prevent dust accumulation on floors, beams, and machinery. Workers should be adequately trained in proper housekeeping.
- Maintenance Schedules: A routine maintenance schedule should include regular inspections and repairs for ventilation systems, ducts, and machines or industrial equipment prone to overheating or sparks.
- Proper Waste Disposal Practices: Employers should train all workers in safe methods for removing and containing combustible materials. They should also enforce these standards.
Lack of adequate housekeeping is one of the most common underlying causes of dust explosions, making this a particular area of concern.
4. Explosion Venting & Suppression Systems
In facilities where dust explosion risks are high, additional protective measures may be necessary to minimize damage if ignition occurs.
Some examples include:
- Explosion Vent Panels: These are designed to rupture in a controlled manner, relieving pressure and directing the blast away from workers.
- Suppression Systems: Automated systems can detect an explosion at its onset and release chemical agents to suppress the blast.
- Isolation Valves: Isolation valves help prevent flame propagation between equipment or duct systems.
These systems are not a substitute for prevention, but they are essential for damage control in high-risk environments.
5. Employee Training & Emergency Preparedness
Even the most advanced systems won’t be effective without a workforce that fully understands the risks and knows how to respond. Employers are responsible for providing workers with ongoing safety training, emergency response drills, and clear signage and communication systems so that workers can quickly receive instructions and information in an emergency. Employees should be educated about the hazards of dust accumulation, trained in safe work practices, and given instruction on how to safely use equipment to help prevent disasters from occurring.
Training should be tailored to specific roles and regularly updated to reflect any changes in processes, materials, or equipment. Furthermore, employers should ensure compliance with safety practices. Turning a blind eye when employees cut corners can have catastrophic consequences.
When Prevention Fails, Accountability Matters
Dust explosions are catastrophic events, impacting hundreds of lives. Victims and their families are the ones left to pick up the pieces of their lives while negligent employers receive nothing more than nominal fines. Even when companies are heavily fined after these incidents, it does nothing to help survivors.
Victims of dust explosions deserve justice. Negligent industrial manufacturers and agricultural companies must be made accountable. By pursuing legal action, those affected can not only seek retribution for themselves but also pressure these entities to take the necessary actions to prevent further tragedies from occurring.
- Categories